Accident Tolerant Fuel
Nuclear energy – the most reliable source of clean non-intermittent electricity in the United States – is under threat from economic factors that could result in the premature closure of many or all of our current reactors. If the U.S. is to maintain this precious resource, which supplies 20% of our electricity needs and 60% of our low-carbon electricity generation, we must invest in cutting-edge technology known as Accident Tolerant Fuel (ATF). ATF can extend the life of current reactors by making them cheaper and nearly meltdown proof, while simultaneously paving the way for advanced nuclear reactors that can greatly exceed the capabilities of the current fleet.
The ATF program was initiated by an act of Congress in 2012 and is funded and overseen by the Department of Energy. GA-EMS is an industry partner on the ATF initiative, providing the ceramic matrix composite fuel rod cladding that replaces the metal cladding used in current fuel rods. This new cladding has an engineered construction using GA-EMS' SiGA® silicon-carbide (SiC) composite, in which the SiC matrix material is reinforced with flexible SiC fiber in much the same way that steel rebar reinforces concrete. This creates an extremely hard and durable material that can withstand the harshest reactor conditions.
GA-EMS' SiGA® cladding allows fuel rods to withstand temperatures of over 3000°F (1700C), more than twice that sustained by the metal cladding used in current reactor cores. In addition, the new cladding is much more chemically stable, virtually eliminating the risk of generating potentially explosive hydrogen during loss-of-cooling accidents. Once deployed at wide scale in the mid-to-late 2020s, these new fuel rods have the potential to greatly improve the safety and economics of current and advanced nuclear reactors.
GA-EMS' ongoing work on SiGA® and ATF has been the subject of a number of scientific papers and presentations. A current list of these can be found here.
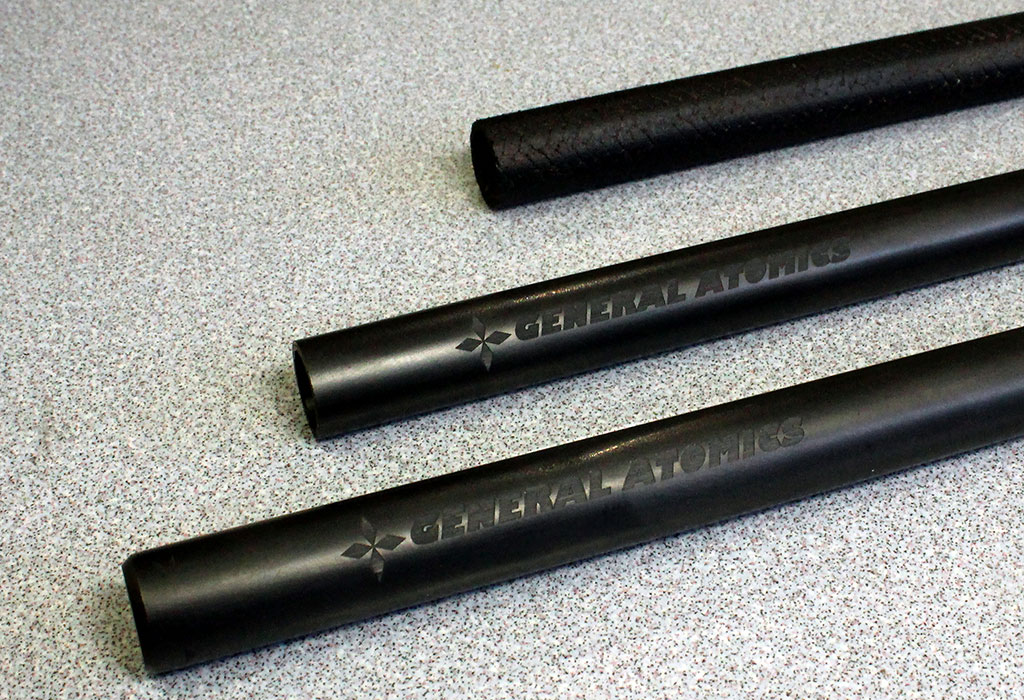
The ATF program was initiated by an act of Congress in 2012 and is funded and overseen by the Department of Energy. GA-EMS is an industry partner on the ATF initiative, providing the ceramic matrix composite fuel rod cladding that replaces the metal cladding used in current fuel rods. This new cladding has an engineered construction using GA-EMS’ SiGA® silicon-carbide (SiC) composite, in which the SiC matrix material is reinforced with flexible SiC fiber in much the same way that steel rebar reinforces concrete. This creates an extremely hard and durable material that can withstand the harshest reactor conditions.
GA-EMS’ SiGA® cladding allows fuel rods to withstand temperatures of over 3000°F (1700°C), more than twice that sustained by the metal cladding used in current reactor cores. In addition, the new cladding is much more chemically stable, virtually eliminating the risk of generating potentially explosive hydrogen during loss-of-cooling accidents. Once deployed at wide scale in the mid-to-late 2020s, these new fuel rods have the potential to greatly improve the safety and economics of current and advanced nuclear reactors.
GA-EMS’ ongoing work on SiGA® and ATF has been the subject of a number of scientific papers and presentations. A current list of these can be found here.